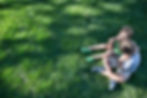
About FNG
For the Next Generation
Our Commitment
At FNG Packaging, our mission goes beyond delivering high-quality packaging solutions - we are dedicated to shaping a more sustainable and innovative future. As a trusted partner, we provide packaging that enhances your brand, meets evolving consumer needs, and supports a greener tomorrow.
Innovative Packaging Solutions for a Stronger Brand
We believe that packaging is more than just a container - it’s a powerful tool that communicates your brand’s values and commitment to quality. That’s why we continuously invest in cutting-edge technology, eco-friendly materials, and process innovation to create solutions that are both functional and environmentally responsible.
Building Strong Partnerships for a Sustainable Future
Beyond our products, we are committed to making a positive impact on our clients, employees, and communities. We foster strong partnerships, uphold ethical business practices, and collaborate with industry leaders to drive meaningful change. Our goal is to be the most responsive, forward-thinking supply partner—helping brands succeed while contributing to a more sustainable world.
The Process

Step 1. Design and Proof
Before production, we provide die lines and artwork. Upon approval, we conduct digital, offset, and cylinder proofing through our Color Management System for accuracy.
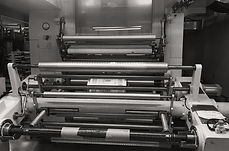
Step 3. Lamination
A two-component adhesive bonds functional films like PET, nylon, aluminum foil, and CPP, enhancing durability and performance.

Step 5. Cut (Slitting)
The laminated rolls are precisely cut to size according to client specifications, ensuring seamless processing in subsequent stages.

Step 2. Printing
Utilizing an rotogravure printing process, we achieve vibrant and accurate colors by employing four-color process printing (CMYK) as well as a wide range of Pantone spot colors. Our high-speed, precision printing technology ensures exceptional quality and efficiency.

Step 4. Aging
After printing and lamination, the material is stored at an optimal temperature for a period of time to stabilize adhesive properties.
_edited_edited.jpg)
Step 6. Bag Making (Converting)
The cured laminated material is heat-sealed and formed into various pouch styles, such as three-side seal and stand-up pouches, meeting diverse packaging needs.
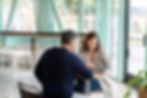